現在、物流コストが上昇するとともに、人手不足に陥っている物流業界。そのような背景から、どの現場においても物流改善は必須となっています。しかし、下記のような悩みを抱えている方も少なくないはずです。
- 物流改善の考え方がわからない
- 物流改善を具体的にどう進めればよいのか
そこで本記事では、物流改善のおける考え方のポイントや具体的な進め方を解説していきます。それだけでなく、物流改善の具体的な事例からアイデア集もまとめたため、初めて物流改善に取り組む方でも、すぐに活用できる知識が身につきます。物流改善でお悩みの方は、ぜひご覧ください。
物流改善の考え方とは?
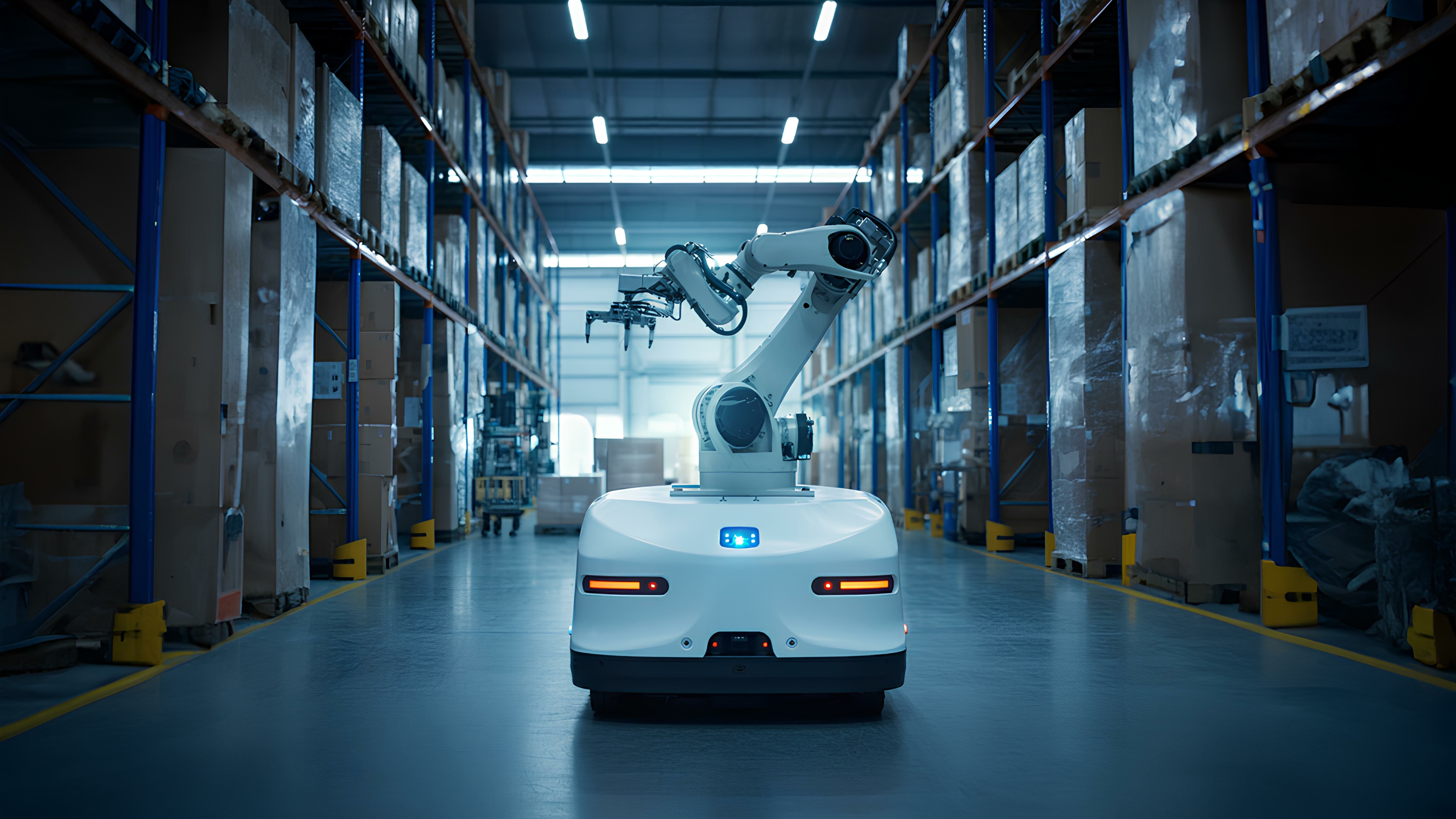
物流業務の効率化や品質向上を目指す「物流改善」は、企業が競争力を高めるうえで重要な取り組みです。そんな物流改善の代表的な考え方は、5つにまとめられます。
- ヒューマンエラーやミスをなくす
- 物流コストを減らす
- 作業効率を改善する
- 作業工程を管理する
- 3M(ムリ・ムダ・ムラ)をなくす
本章では、物流改善を進めるための具体的な考え方や重要なポイントを解説します。
ヒューマンエラーやミスをなくす
物流業務におけるヒューマンエラーは、作業効率の低下や顧客満足度の低下を引き起こす要因です。例えば、類似商品を取り違える、品番を見間違える、作業手順を間違えるといった問題がよく発生します。
これを防ぐためには、業務プロセスを見える化し、バーコードやRFIDなどの技術を活用して作業の正確性を高めることが有効です。また、マニュアルの作成や作業環境の改善、スタッフの負担軽減も、ヒューマンエラー削減につながります。
物流コストを減らす
物流コスト削減は、収益性向上に直結する重要な施策です。主なコスト要素は以下の4点にまとめられます。
- 輸送費
- 保管費
- 荷役費
- 物流管理費
上記の物流コストを見直し、無駄を排除することが求められます。例えば、輸送網の集約やモーダルシフトを活用することで、輸送効率を上げつつコストを抑えることが可能です。コスト削減には現状のコスト構造を把握し、改善余地を分析することが不可欠です。
作業効率を改善する
作業効率を向上させるには、現場の動線や作業フローの見直しが必要です。特に、習慣化された非効率な作業を削除することで大きな効果を得られます。例えば、作業工程を細分化し、各スタッフに明確な役割を与えることで効率化が図れます。場合によってはAGV(自動搬送車)のような自動化に着手するのも一つの案でしょう。
また、倉庫内の動線を最適化することで、作業の無駄を削減できます。これには、作業内容のデータ化や動線の可視化ツールを活用すると効果的です。
作業工程を管理する
物流改善の第一歩は、現状を正確に把握し、問題点を特定することです。「誰が」「どこで」「何を」「どのように」行っているのかを明確にすることで、改善点が浮き彫りになります。
作業記録をデジタル化し、工程の進捗をリアルタイムで把握する仕組みを構築することで、ミスの早期発見と解決が可能になります。また、管理の一環として、定期的な業務分析や問題点の共有を行うことが重要です。
3M(ムリ・ムダ・ムラ)をなくす
物流現場では、3Mが問題となることが多いです。3Mとは、製造業における効率や品質を低下させる要因を言い表すときに使われる言葉です。具体的には、以下の3点となります。
- ムリ(過剰な負荷)
- ムダ(不要な作業)
- ムラ(作業のばらつき)
これらの課題に対処するには、作業量とリソースのバランスを見直すとともに、自動化技術を導入することが効果的です。例えば、倉庫内のピッキング作業にマテリアルハンドリング機器を導入すれば、作業効率が向上します。
物流改善の代表的な事例集3選
物流改善は、効率化やコスト削減、生産性向上を目指す上で欠かせない取り組みです。本節では、物流改善に成功した具体的な事例集を3つご紹介します。それぞれの物流改善事例を通じて、現場の課題解決や成果を詳しく解説します。
作業の効率化事例:ヤマト運輸
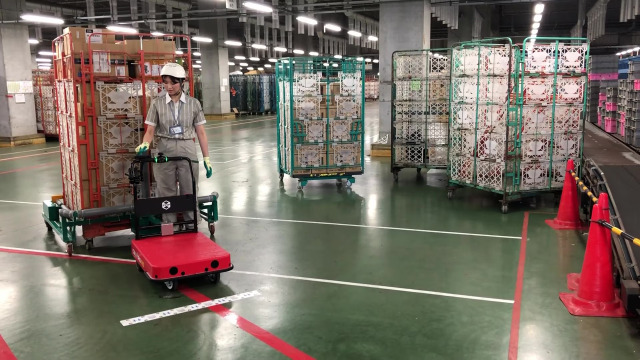
物流の生産性向上事例の一つがヤマト運輸です。ヤマト運輸では、広大なターミナルで荷物の仕分けや積み込み作業を行う際、ロールボックスパレットを人手で搬送していました。この方法では、作業員の負担が大きく、省人化と省力化が必要とされていました。
そこでヤマト運輸は、自動搬送ロボット「CarriRo®」を導入。このロボットにより、ロールボックスパレットの搬送を自動化し、作業員の負担を軽減しながら作業の効率化を実現しました。また、柔軟な搬送ルートの設定が可能で、運用変更にも柔軟に対応できる点が高く評価されました。
- ムダの削減:片道搬送後の「手ぶら戻り」を解消し、作業効率が大幅に向上
- 作業環境の改善:搬送作業の負担が軽減され、搬送ルートが明確になったことで安全性が向上
作業工程の改善事例:コマツ物流株式会社
コマツ物流株式会社では、海外向けのボルト梱包作業が従業員にとって大きな負担となっていました。特に「載せ替え作業」や「長い運搬動線」が生産性を下げる主な要因でした。
同社では、仕分け時に輸出容器の底板へ直接仕分ける方法に変更し載せ替え作業を廃止。さらに、スペースレイアウトを「コの字型」に再設計することで、作業動線を短縮しました。
主な成果は以下のとおりです。
- 作業時間の短縮
- 苦渋作業の大幅な削減
参考:2023年度「物流改善賞」が決定! | 公益社団法人日本ロジスティクスシステム協会
3Mの削減事例:SBS東芝ロジスティクス
SBS東芝ロジスティクスでは、作業者が「見る・探す・考える・待つ・屈む」といったストレスに悩まされていました。特にムリ・ムダ・ムラ(3M)が多く見られ、現場全体で改善が急務となっていました。
同社では、作業現場を詳細に可視化するため、ビデオチェックを活用。その結果、「動線設計の見直し」「作業指示の簡素化」「作業環境の最適化」の各種物流改善につながりました。
3Mの排除により、次のような成果を達成しました。
- 作業ストレスの軽減
- 作業時間の短縮
- 作業品質の向上
参考:全日本物流改善事例大会 2024 において「優秀物流改善賞」を受賞|SBS東芝ロジスティクス株式会社
物流改善の進め方5STEP
物流改善が重要な取り組みだとわかっていただけたかと思います。ここからは効率的に物流改善を進めるための具体的な5つのステップを解説します。
- 現状を把握する
- 物流改善の計画を立案する
- 物流改善の施策を実施する
- 施策の成果を検証する
- 継続的な改善に取り組む
①:現状を把握する
現場の現状を正確に把握することが物流改善の第一歩です。物流現場では、3M(ムリ・ムダ・ムラ)といった非効率的な作業が多く見られます。人為的ミスや工程の属人化も改善の障害になる場合があります。そのため、誰が、どこで、どのような作業をしているのかを把握し、課題を明確にすることが重要です。
「現場が忙しい中で現状把握に時間を割くのは難しい」と感じる方もいるかもしれません。ただ、現状把握によって課題が明確になれば、長期的には効率が向上し、結果的に時間やコストを削減できます。データや現場からのフィードバックを活用し、正確な情報をもとに課題を洗い出しましょう。
②:物流改善の計画を立案する
物流の課題が明確になったら、具体的な改善計画を立案することが重要です。物流改善を成功させるには、実現可能な目標設定と工程管理が欠かせません。具体的なステップを設けることで進捗が見えやすくなり、現場の混乱を防ぐことができます。
- 課題の優先順位付け
- 課題に対する施策の選定
- 施策に対するコスト・見込み効果の分析
上記のステップに沿うことで、現場の意見を取り入れながら、実現可能で効果的な計画を策定ができます。
③:物流改善の施策を実施する
続いて、計画をもとに物流改善の具体的な施策を現場で実施します。施策を実施する際は、試験導入から始めましょう。改善案を一部エリアや限定的な条件で試験運用し、結果を確認します。
データ結果や作業現場のスタッフ、関係者からの意見を集め、改善案をブラッシュアップします。そして、成功が確認された施策を物流・倉庫の全体に展開していきます。
④:施策の成果を検証する
物流改善の施策を実施したら、その成果をデータで検証し、目標に対する進捗を確認しましょう。なお、成果を検証する際には定量的な分析と定性的な分析が必要です。
- 定量的な分析:配送時間、コストなどを数値的に分析する
- 定性的な分析:現場スタッフや関係やからのフィードバックを収集・分析する
施策が計画通りに進行しているか、期待した効果が得られているかを確認します。必要に応じて軌道修正を行うことで、物流改善の成功率をさらに高められます。
⑤:継続的な改善に取り組む
物流改善は一度で完了するものではなく、継続的な取り組みが必要です。なぜなら、物流現場の課題は日々変化するためです。新たな問題が発生する可能性もあるため、PDCAサイクルを回し続けることが重要です。
場合によっては、IoTやAI、ロボティクスなど新しい技術やトレンドを導入することも視野に入れましょう。弊社が提供する自動搬送ロボット「CarriRo®」もその一例になります。
物流改善・倉庫改善の具体的なアイデア
以下では、物流改善や倉庫改善の具体的なアイデアを共有します。ご参考にしてください。
※ここで掲載しているのは代表的な例であり、他にも物流改善施策は多く存在します。
自動搬送ロボットを導入して省人化を図る
物流業界では、人手不足が大きな課題となっています。この問題を解決するためには、自動搬送ロボット(AGV)の導入が有効です。自動搬送ロボットは柔軟なルート設定が可能で、簡単な操作で運用を始められます。これにより現場作業者の負担が軽減され、物流の生産性が向上します。
導入を検討する際は、自社の物流現場に適した運用方法を設計しましょう。導入を検討している方は、弊社が提供する自動搬送ロボット「CarriRo®」についてもお気軽にお問い合わせください。
ハンディターミナルを導入する
ハンディターミナルとは、バーコードやQRコードをスキャンしてデータを収集する携帯型のデバイスです。簡単な操作で在庫情報や出荷データを記録・更新することができます。スキャン作業は手作業になりますが、操作が直感的で習得しやすい点やデータがリアルタイムで確認・共有できる点、幅広い用途がある点がメリットとなります。
目視や手入力に頼るデータ管理を省けるため、ミスの抑制だけでなく、作業時間の短縮にもつながります。また、導入コストが比較的安い点もポイントです。
RFIDを導入する
RFID(Radio Frequency Identification)は、物流改善に役立つ技術の一つです。電波を利用してタグに埋め込まれた情報を非接触で読み取る技術で、複数のタグを一括で読み取れるため、作業時間を大幅に削減できます。
さらに、障害物があっても通信できる特性を活かし、梱包された状態や高い棚の商品でも正確なデータを取得可能です。この技術は誤出荷や在庫不足を防ぎ、作業者の負担軽減にもつながります。
倉庫管理システム(WMS)を導入する
倉庫管理システム(WMS)の導入は、物流業務の効率化に大きく貢献します。WMSを活用することで、商品の入出庫、在庫管理、ピッキング、配送手配などを一元管理できます。この一元化により、作業ミスや在庫ロスが大幅に削減されます。
さらに、データを基に最適な人員配置や動線設計が可能になり、3M(ムリ・ムダ・ムラ)を排除できます。WMSを導入した企業では、作業効率が飛躍的に向上したという物流改善事例もあります。業務を見える化することで、従業員の働きやすさも向上し、物流改善につながります。
一部作業をアウトソーシングする
人手不足や業務量の増加に対応するには、一部の業務をアウトソーシングすることも効果的です。ピッキングや梱包作業、配送業務などを専門業者に委託することで、コア業務に集中できる環境を整えられます。なお、資格を持っている物流現場改善士に相談するのも一つの手でしょう。
アウトソーシングを考える場合には、同時に自動化技術の導入も検討しましょう。短期的なコスト削減や柔軟性が求められる場合はアウトソーシングが適していますが、長期的な効率化や競争力の強化を目指す場合は自動化技術の導入が適している場合があります。
まとめ:企業の競争力を高めるためにも物流改善を
本記事では、構内物流の改善や倉庫における物流改善の考え方や進め方、代表的な事例を解説しました。この記事を読むことで、物流現場での非効率や課題を解決するための具体的なアプローチが明確になったのではないでしょうか。
物流改善のポイントをおさらいします。
- 「物流改善」は、企業が競争力を高めるうえで重要な取り組みである
- 自動化技術、機械、管理システムなどの導入が求められる
- 物流の改善には、PDCAサイクルを回して継続的に改善することが重要である
今回紹介した取り組みを実践することで、物流現場の効率化やコスト削減が実現し、企業全体の競争力を高めるかもしれません。
弊社(コラボット株式会社)も「CarriRo®」という自動搬送ロボットを開発・提供しております。もし物流改善にお悩みで搬送の自動化に興味がある方は、お気軽にお問い合わせください。詳しい説明からお見積り、ちょっとした疑問まで受け付けております。